Heavy-duty split leather welding gloves are specialized personal protective equipment (PPE) designed to offer maximum hand protection during welding and other high-temperature industrial processes. Welding involves handling hot metal and generating sparks, so welding gloves are essential to prevent burns, cuts, and abrasions while maintaining dexterity for precise work.
Here are some key features and characteristics of heavy-duty split leather welding gloves:
Material: Heavy-duty split leather welding gloves are typically made from high-quality cowhide or other types of split leather. Cowhide split leather is preferred for its durability, heat resistance, and ability to withstand sparks and molten metal splatter.
Reinforcements: These gloves often feature additional reinforcements on vulnerable areas like the palm, thumb, and index finger to enhance protection against abrasion and wear.
Length: Welding gloves are usually longer than regular work gloves to provide extended coverage, protecting the wrists and lower arms from heat and sparks.
Heat resistance: Heavy-duty welding gloves are specifically designed to offer high heat resistance, ensuring that they can withstand the extreme temperatures produced during welding operations.
Stitching: The gloves are often sewn with Kevlar thread, which provides added heat resistance and durability, reducing the risk of thread melting during welding.
Lining: Some heavy-duty welding gloves come with a soft lining, such as fleece or cotton, to improve comfort during extended use and to absorb sweat.
Cuff closure: Many welding gloves have a cuff closure system, such as Velcro or snap buttons, to secure the gloves tightly around the wrists and prevent debris or sparks from entering the gloves.
Dexterity: While welding gloves prioritize protection, efforts are made to ensure they offer reasonable dexterity, allowing welders to handle tools and materials effectively.
When using heavy-duty split leather welding gloves, it’s crucial to adhere to proper safety procedures, including regular inspections for signs of wear, tears, or other damage. Gloves that show signs of damage should be replaced immediately to maintain their effectiveness.
Welders should also consider the specific welding process and materials they will be working with to choose the appropriate type of gloves. For instance, different welding techniques (e.g., MIG, TIG, Stick welding) may require different levels of heat resistance and dexterity. Consulting with safety experts and following industry best practices will ensure the right choice of gloves for a safe and productive welding environment.
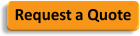